We understand that maintaining the highest standards of cleanliness and quality is critical in the glass production and inspection process. To meet the growing demands of precision glass components used across various industries, we have established a state-of-the-art cleanroom designed to ensure top-notch product quality and reliability.
Our Cleanroom Capabilities
Our cleanroom is equipped with cutting-edge facilities to ensure maximum cleanliness and precision during every stage of the production and inspection process. The cleanroom is structured into specialized areas to ensure optimal environmental conditions for each process:
Cleanroom configuration:
- Cleanliness: Class 1000
- Temperature: 22±2°C
- Humidity: 40–60%
- Air Changes: ≥20 times per hour for Class 1000 areas
- Pressure Difference: ≥5 Pa between the main production area and adjacent rooms, ≥10 Pa between cleanroom and standard rooms
- Illumination: 300 Lux in clean areas
- Noise Level: ≤60 dB(A) in purification areas

Equipment Zone:
This area houses vital systems, including the air purification and HVAC units, high-purity water and gas supply systems, and cooling/heating equipment to ensure continuous, controlled conditions in the cleanroom.
Specialized Cleaning and Inspection Processes:
we are committed to maintaining the highest standards of cleanliness throughout every stage of production. To ensure this, we employ advanced cleaning systems, including ultrasonic baths that remove even the most microscopic contaminants from glass components before they are packaged. These ultrasonic systems operate across multiple stages, each tuned to specific frequencies for deeper and more effective cleaning.
We also prioritize the protection of both the glass components and the clean room itself by using plastic and stainless steel containers for transportation. This prevents contamination from materials like cardboard or wood that may introduce particles or residues into the sensitive environment.
Applications in Optical and Microelectronics:
Our clean room capabilities are especially crucial for industries such as optics and microelectronics, where product cleanliness directly impacts performance. Whether manufacturing optical lenses, microelectronic substrates, or medical device components, we ensure that all glass parts undergo thorough cleaning and inspection. After cleaning, they are packaged within the controlled environment of the clean room, preserving their purity and ensuring that they are ready for direct use in the customer’s production line—no additional cleaning required.
Fabrication & Cleaning Integration
Every step of the fabrication process can impact the cleanliness of the final product. To minimize contamination, we have integrated advanced cleaning technologies at key stages of production. Our process includes mechanical scrubbing, ultrasonic cleaning, and thorough inspection, all of which are conducted in a controlled environment to ensure optimal cleanliness.
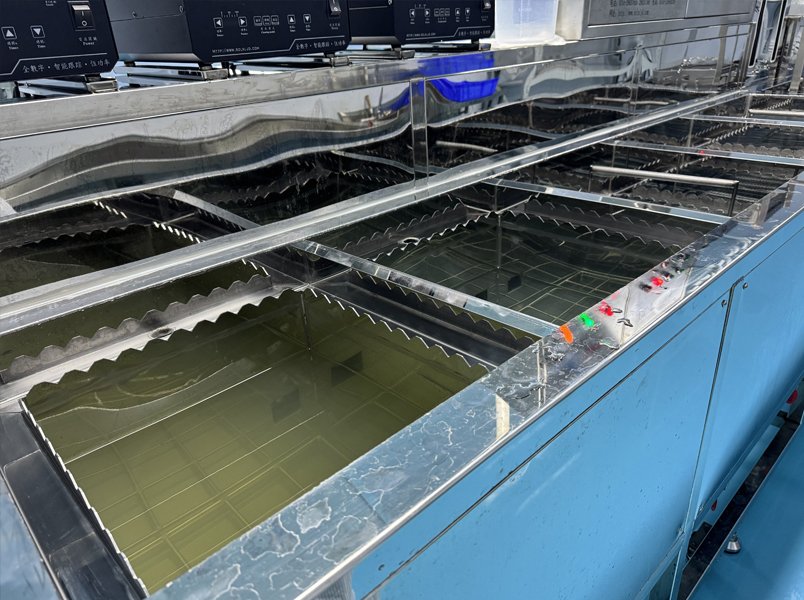
Step-by-Step Cleaning Process
- Mechanical Wash
- The first step involves a Mechanical Scrub to remove large particulate contaminants such as grinding residues, polishing compounds, and other debris that are not easily cleaned by ultrasonic methods. This stage ensures the glass surface is free from heavy contamination before proceeding to more delicate cleaning processes.
- Ultrasonic Wash 1
- For glass components with a diagonal size of less than 300mm, we use a 10-stage Ultrasonic Cleaning Line. The stages include:
- Stage 1 & 3: Optical soap is used to break down stubborn contaminants.
- Stage 2 & 4-9: DI (Deionized) water rinses progressively filter out particulate matter.
- Final Stage: An IPA vapor bath removes any residual moisture, ensuring the glass is completely clean and ready for inspection.
- For glass components with a diagonal size of less than 300mm, we use a 10-stage Ultrasonic Cleaning Line. The stages include:
- Ultrasonic Wash 2
- For larger glass components, up to 550mm in diameter, we operate a 6-stage Ultrasonic Wash Line. This line runs in parallel with the first, featuring a slower pull and filtered air drying at the end to ensure that larger pieces also meet our rigorous cleanliness standards.
Every order, whether a prototype, small batch or high volume production, goes through a strict quality control phase.

Tools which we employ to aid in these quality checks are:
- Optical comparator
- High power microscope
- interferometer
- Optical plane
With these specialized tools, we are able to carry out detailed inspection at every stage of production to ensure that every batch of optical components meets industry standards and meet the strict requirements of our customers.
Why choose US:
At lighting GLASS, we are committed to helping customers save time and costs by optimizing optical manufacturing and shipping processes. With a wide range of automatic ultrasonic cleaning systems. And strict quality control ensures that the glass we supply meets extremely high cleaning standards.
We constantly innovate and strive to improve the quality of our services. If you have optical cleaning and packaging needs, please contact us. We will provide the most suitable solution according to your specific requirements to ensure that your project is completed on time and with good quality.