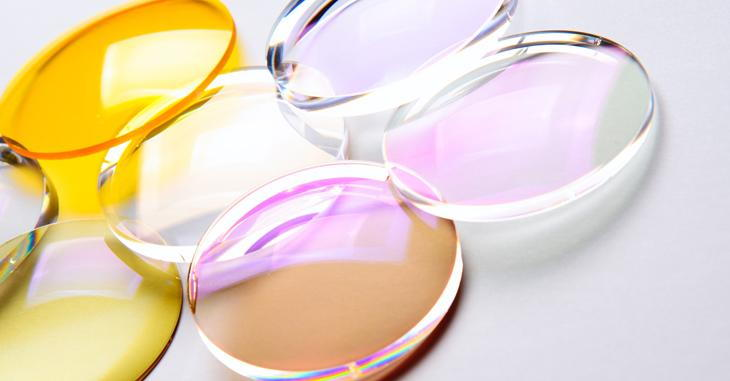
Optical glass and lenses are essential components in various industries, from eyeglasses to camera systems and scientific instruments. In this article, we will explore the different types of optical lenses, the materials used in their production, and their wide-ranging applications. We will also discuss the role of optical glass manufacturers in producing high-quality components for a variety of uses.
What is Optical Glass?
Optical glass is a type of glass that is specifically designed for use in optical applications. It has special properties, such as high clarity, precision, and the ability to manipulate light, which makes it ideal for use in optical instruments. Unlike regular glass, optical glass is made with specific compositions that ensure minimal distortion and maximum transparency.
How Are Optical Lenses Made?
The process of making optical lenses involves several steps to ensure they meet precise standards. Here’s an overview of how custom optical lenses are made:
Material Selection: The first step is selecting high-quality optical glass or other materials that meet the specific requirements for the lens, such as refractive index, dispersion, and durability.
Cutting and Shaping: Once the material is selected, it is cut into the desired shape, often using advanced machinery and CNC technology. The optical lens is shaped to precise dimensions.
Grinding and Polishing: After the initial shaping, the lens undergoes grinding and polishing to ensure its surface is smooth and free of imperfections.
Coating: To enhance the lens’ performance, a coating may be applied to improve light transmission, reduce reflections, or protect the lens from scratches.
Testing: Each lens is carefully tested for optical properties, such as clarity, curvature, and focal length, to ensure it meets the required standards.
Types of Optical Lenses and Filters
Optical lenses are classified into several types based on their function and design. Here are a few common one
Supplemental Content: Classification and Characteristics of Optical Lenses
1. Common Types of Optical Lenses (Expanded):
- Convex Lens: Used to converge light, commonly found in camera lenses and telescope objectives.
- Concave Lens: Diverges light, used for myopia correction or compensating aberrations in optical systems.
- Fresnel Lens: Lightweight design with concentric ring structures replacing curved surfaces, used in lighthouses and projectors.
- Aspheric Lens: Eliminates spherical aberrations, improving imaging quality, widely used in high-end cameras and medical devices.
- Optical Filters: Examples include infrared cut-off filters (IR Cut) and bandpass filters, used to isolate specific wavelengths in sensors and spectrometers.
2. Classification and Properties of Optical Glass
Optical glass is categorized by refractive index (n) and dispersion (Abbe number, Vd):
- Crown Glass: Low refractive index (n < 1.6), high Abbe number (Vd > 50), low dispersion, ideal for achromatic designs (e.g., doublet lenses).
- Flint Glass: High refractive index (n > 1.6), low Abbe number (Vd < 50), high dispersion, used to enhance light-bending capabilities.
- Specialized Materials: Calcium fluoride (CaF₂) for UV lenses, fused silica for high-temperature and laser-resistant applications.
3. Critical Role of Coating Technologies
- Anti-Reflective (AR) Coating: Reduces surface reflections (as low as 0.1% per surface) via multilayer interference, improving light transmission.
- Hydrophobic/Oleophobic Coating: Fluoropolymer-based coatings prevent liquid adhesion, used in outdoor optics.
- Hard Coating: Diamond-like carbon (DLC) coatings enhance scratch resistance.
Industry FAQs and Solutions
Q1: How to balance refractive index and Abbe number (dispersion) in material selection?
A1: High-index materials reduce lens curvature (lowering thickness) but increase chromatic aberration due to low Abbe numbers. Use crown glass (low n, high Vd) combined with flint glass (high n, low Vd) to design achromatic doublets, such as cemented lens groups in camera lenses.
Q2: How to control surface accuracy during lens manufacturing?
A2:
- Use interferometers to measure surface form accuracy (RMS < λ/20, λ=632.8 nm).
- Employ advanced polishing techniques like magnetorheological finishing (MRF) or ion beam figuring (IBF) to achieve sub-nanometer surface roughness.
Q3: How to ensure optical system stability in high-temperature or high-humidity environments?
A3:
- Select low thermal expansion materials (e.g., ULE glass).
- Implement environmental sealing (nitrogen purging or waterproof adhesives).
- Ensure coatings pass 85°C/85% humidity aging tests (e.g., MIL-STD-810 standards).
Q4: How to reduce manufacturing costs for optical components?
A4:
- Adopt precision molding for mass production, minimizing grinding/polishing steps.
- Use standardized lens libraries (e.g., ISO 10110) to reduce customization.
- Optimize coating processes (e.g., batch coating over single-piece coating).
Cutting-Edge Technologies and Trends
- Freeform Optics: Asymmetric designs break rotational symmetry limits, enabling AR/VR headsets and automotive HUDs.
- Metasurfaces: Nanostructure arrays create ultrathin flat lenses, revolutionizing traditional optics.
- Eco-Friendly Materials: Development of lead/arsenic-free glass (e.g., H-ZLaF75) to comply with RoHS and REACH regulations.
Advice for Professionals
- Design Phase:
- Simulate light paths using Zemax/Code V to avoid redesigns.
- Prioritize proven materials (e.g., Schott N-BK7, Ohara S-TIH53) to mitigate risks.
- Production Phase:
- Regularly calibrate equipment (e.g., CNC machine temperature compensation).
- Maintain cleanroom standards (Class 100 or better) to prevent contamination.
- Testing Phase:
- Validate resolution with MTF (Modulation Transfer Function) testing.
- Use spectrophotometers to verify coating spectral performance.
Expanded Application Examples
- Medical Field: Endoscopes utilize gradient-index (GRIN) lenses (<1mm diameter) for high-resolution in-body imaging.
- Autonomous Vehicles: LiDAR systems employ 1550 nm wavelength lenses with custom IR coatings.
- Consumer Electronics: Smartphone camera modules adopt 7-element plastic (7P) aspherical designs for enhanced low-light performance.