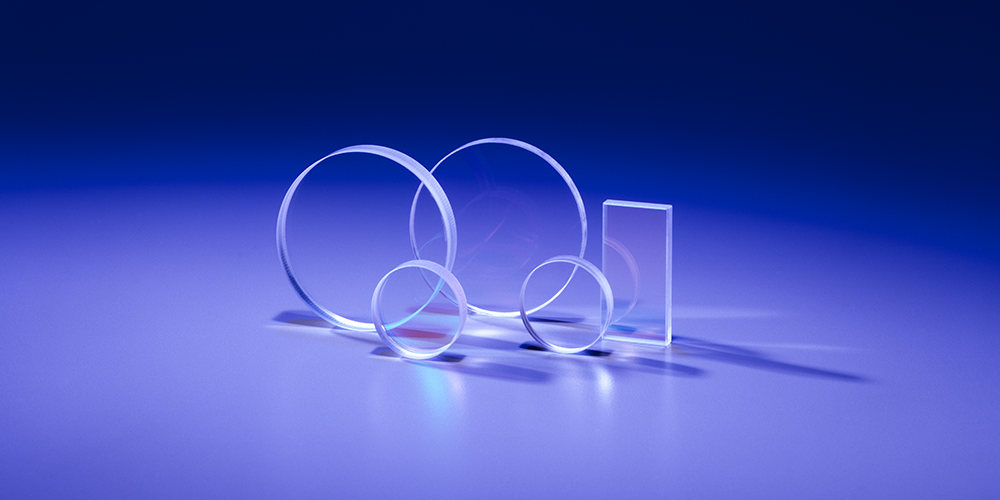
In the rapidly evolving world of UV technology, selecting the best UV glass for your applications is crucial for achieving optimal performance, safety, and longevity. From advanced sterilization systems to precision spectroscopy equipment, the choice of UV resistant glass material directly impacts system efficiency, operational costs, and end-user satisfaction. This comprehensive guide explores the critical factors that determine which glass types excel in UV applications across various industries.
Why UV Applications Need Specialized Glass Materials
Standard glass materials fail dramatically when exposed to ultraviolet radiation, particularly in the UVC spectrum (200-280nm). Regular soda-lime glass blocks over 90% of UV light below 300nm, making it unsuitable for applications requiring UV transmission glass. More critically, prolonged UV exposure causes structural degradation in conventional glass, leading to discoloration, reduced transparency, and mechanical failure.
UV resistant glass materials are engineered specifically to withstand intense ultraviolet radiation without degradation. These specialized UV glass materials maintain optical clarity under UV exposure for extended periods, ensuring consistent performance in demanding applications. The molecular structure of UV-grade glass prevents the formation of color centers that would otherwise compromise transmission efficiency.
Professional UV applications require materials that not only transmit UV light efficiently but also resist solarization – the gradual darkening that occurs when UV glass is exposed to high-energy photons. This resistance is achieved through careful selection of raw materials and precise manufacturing processes that eliminate UV-absorbing impurities.
Understanding UV Transmission Glass Properties
The effectiveness of UV transmission glass depends on several critical factors. High-transmission UV glass must maintain consistent optical properties across varying temperatures and exposure durations. UVC-transparent materials require exceptional purity levels to prevent absorption losses that would compromise system performance.
Low solarization glass for UV applications undergoes specialized manufacturing processes that eliminate trace impurities responsible for UV-induced darkening. This characteristic is particularly important for precision UV optical components where even minor transmission losses can significantly impact performance.

Comprehensive UV Glass Types Comparison: Fused Silica vs Borosilicate vs Modified Soda-Lime

Fused Silica: The Premium UV Glass Solution
Fused silica represents the gold standard in UV glass applications, offering unmatched performance in UVC sterilization and precision optical systems. This UV resistant glass achieves exceptional transmission rates exceeding 90% in the UVC range, making it the preferred choice for germicidal applications and high-precision UV optical window installations.
The manufacturing process of optical-grade fused silica involves flame fusion or electric fusion techniques that eliminate virtually all metallic impurities. This purity level is essential for maintaining consistent UV transmission glass performance, as even trace amounts of iron or other metals can significantly reduce UV efficiency. UV-resistant quartz glass maintains its optical properties even under intense UVC exposure, providing reliable performance for over 20,000 operational hours.
Key advantages of fused silica for UV applications:
- Exceptional UVC transmission (>92% at 254nm)
- Superior thermal stability (softening point: 1680°C)
- Minimal thermal expansion (0.55×10⁻⁶/K)
- Outstanding chemical resistance
- Long operational lifetime in UV environments

Borosilicate Glass: The Balanced UV Glass Alternative
Borosilicate UV glass offers a compelling middle ground between cost and functionality for many UV applications. While not matching fused silica’s transmission efficiency in the deep UV range, borosilicate UV resistant glass provides excellent performance for UV-A and UV-B applications with transmission rates of 85-90% in the 280-400nm range.
This UV transmission glass type demonstrates superior thermal shock resistance, making it particularly suitable for high-temperature UV processes where rapid temperature changes occur. Modern borosilicate formulations achieve reliable UV glass performance while maintaining cost advantages for medium-volume applications.
Borosilicate UV glass characteristics:
- Good UV-A and UV-B transmission (85-90% at 280-400nm)
- Excellent thermal shock resistance
- Moderate thermal expansion (3.25×10⁻⁶/K)
- Cost-effective for many UV applications
- Reliable performance for 5,000+ operational hours

Modified Soda-Lime Glass: Specialized UV Applications
While standard soda-lime glass blocks most UV radiation below 300nm, specialized UV transparent glass variants of soda-lime compositions can achieve reasonable transmission in the near-UV range. These modified formulations provide cost advantages for high-volume UV-A applications where some UV blocking is actually beneficial.
UV glass manufacturers have developed enhanced soda-lime compositions that improve UV transmission while maintaining the economic benefits of traditional glass production methods. These materials serve specific niches in the UV glass market where extreme performance isn’t required.
Detailed Performance Comparison Table
Property | Fused Silica | Borosilicate 3.3 | Modified Soda-Lime |
UVC Transmittance (254nm) | 92% | <5% | 0% |
UVB Transmittance (300nm) | 90% | 80% | 15% |
UVA Transmittance (365nm) | 88% | 85% | 75% |
CTE | 0.55×10⁻⁶/K | 3.25×10⁻⁶/K | 9×10⁻⁶/K |
Softening Point | 1680°C | 820°C | 720°C |
UV Radiation Lifetime | >20,000 hours | 5,000 hours | <800 hours |
Relative Cost | High | Medium | Low |
Solarization Resistance | Excellent | Good | Poor |
UV Glass Selection Guidelines by Application
UVC Applications (200–280 nm)
For germicidal and sterilization applications, only fused silica provides the high transmission and long-term stability required. UV-resistant quartz glass maintains performance under intense UVC exposure, making it essential for medical sterilization, water treatment, and air purification systems.
UVB Applications (280–315 nm)
High-temperature applications (>150°C): Use fused silica for superior thermal resistance and consistent UV transmission glass performance.
Moderate-temperature applications (<150°C): Borosilicate UV glass offers cost-effective reliability with good transmission characteristics.
UVA Applications (315–400 nm)
Cost-sensitive projects: Modified soda-lime UV glass provides adequate performance for basic UV-A applications.
Performance-critical applications: Borosilicate or fused silica UV optical window materials deliver superior consistency and longevity.
Industrial Applications of UV Glass Technologies

UV Sterilization Systems
Germicidal UV systems require quartz UV tube components and UV optical window materials that deliver maximum UVC output for pathogen destruction. These applications demand UV transmission glass with transmission rates above 85% at 254nm, the peak germicidal wavelength. UV-resistant quartz glass tubes and windows ensure that sterilization systems operate at designed efficiency levels while maintaining structural integrity under continuous UV exposure.
The manufacturing of sterilization lamp quartz UV tube components requires precise control of fused silica purity and wall thickness. Even minor variations can create hot spots or reduce UV output, compromising sterilization effectiveness. Professional-grade UV glass for these applications undergoes rigorous quality testing to ensure consistent performance across the entire UV spectrum.

UV Curing and Industrial Processing
Industrial UV curing processes require specialized UV glass cover materials that combine high UV transmission glass properties with mechanical durability. These applications typically operate in the UV-A range (315-400nm) where properly formulated borosilicate or specialized fused silica provides optimal performance.
The thermal cycling inherent in UV curing systems places significant stress on UV resistant glass components. Materials must withstand repeated heating and cooling cycles while maintaining dimensional stability and optical properties. Advanced UV glass formulations incorporate thermal stress relief techniques to extend component life in demanding production environments.

Precision UV Optical Systems
Analytical instruments require UV optical window components for spectrometers that maintain exceptional optical clarity across broad UV ranges. These applications demand precision UV optical components with minimal absorption, low fluorescence, and excellent surface quality to ensure accurate spectral measurements.
Spectroscopic applications often require custom UV glass specifications, including specific transmission curves, surface flatness tolerances, and anti-reflective coatings. The interaction between UV radiation and UV optical window surface treatments requires careful consideration to prevent coating degradation that would compromise measurement accuracy.
Advanced Considerations in UV Glass Selection
The choice between UV filter glass vs UV pass glass depends on specific application requirements. Filter glass blocks unwanted UV wavelengths while transmitting desired ranges, while pass glass maximizes transmission across broad UV spectra. Understanding these distinctions is crucial for optimizing system performance.
Optical properties of UV grade fused silica vary significantly based on manufacturing methods and purity levels. Flame-fused quartz offers different characteristics compared to electrically fused materials, affecting transmission, homogeneity, and mechanical properties. Professional applications require careful matching of material properties to performance requirements.
Precision glass machining for UV systems involves specialized techniques to minimize surface damage and maintain optical quality. Diamond tooling, controlled environments, and post-processing treatments ensure that machined components meet stringent optical specifications. Surface roughness and edge quality directly impact UV transmission efficiency and system performance.
The comparison of quartz vs borosilicate for UV applications must consider total cost of ownership, including initial material costs, processing requirements, and expected service life. While quartz offers superior UV performance, borosilicate may provide better value for applications with moderate UV requirements and thermal stress considerations.
Choosing the Right UV Glass Supplier for Your Application
Looking for a custom UV glass manufacturer? Whether you need fused silica optical components, UVC quartz tubes, or machined borosilicate parts, our factory supports global clients with precision, reliability, and custom engineering.
Contact us today to discuss your UV application needs and discover how our expertise can optimize your next UV system project.
FAQ
What makes UV glass different from regular glass?
UV glass is specifically engineered to transmit ultraviolet radiation efficiently while resisting degradation. Unlike regular glass that blocks most UV light, UV transmission glass maintains high transmission rates across UV wavelengths and resists solarization (darkening) under UV exposure.
Which UV glass type offers the best transmission?
Fused silica provides the highest UV transmission glass performance, achieving over 92% transmission at 254nm. This UV-resistant quartz glass maintains exceptional clarity throughout the entire UV spectrum, making it ideal for critical applications.
How long does UV resistant glass last?
The lifetime of UV resistant glass varies by material type and application conditions. Fused silica can operate for over 20,000 hours under intense UVC exposure, while borosilicate UV glass typically provides 5,000+ hours of reliable service.
Can UV glass be customized for specific applications?
Yes, precision UV optical components can be manufactured to meet specific transmission, geometric, and performance requirements. Custom UV optical window designs, quartz UV tube configurations, and specialized coatings are available from qualified manufacturers.
What’s the difference between quartz and fused silica for UV applications?
Fused silica and UV-resistant quartz glass are essentially the same material – high-purity silicon dioxide. The terms are often used interchangeably in UV glass applications, with both offering exceptional UV transmission and resistance properties.
How do I select between different UV glass materials?
UV glass selection depends on wavelength requirements, operating temperature, budget constraints, and performance specifications. UVC applications require fused silica, while UV-A applications may perform well with borosilicate UV transmission glass.
What causes UV glass to degrade over time?
UV glass degradation occurs through solarization – the formation of color centers when high-energy photons interact with glass impurities. Low solarization glass for UV applications uses ultra-pure materials and specialized manufacturing to minimize this effect.
Are there cost-effective alternatives to fused silica?
For applications not requiring extreme UV transmission glass performance, borosilicate glass offers a cost-effective alternative with good UV-A and UV-B transmission. Modified soda-lime UV glass provides the most economical option for UV-A applications.
Conclusion: Optimizing Your UV Glass Selection
Selecting the optimal UV glass material for your applications requires careful consideration of transmission requirements, operating conditions, and performance specifications. Whether your application demands the ultimate performance of high-transmission UV glass like fused silica or the cost-effectiveness of specialized borosilicate UV resistant glass, understanding material properties and supplier capabilities is essential for project success.
The future of UV glass technology continues to evolve with new materials and manufacturing techniques that expand the possibilities for UV applications. By staying informed about UVC-transparent materials developments and working with experienced UV glass suppliers, you can ensure your UV systems deliver optimal performance and reliability.